Feature Review: HYD/FUEL
Posted July 23, 2021
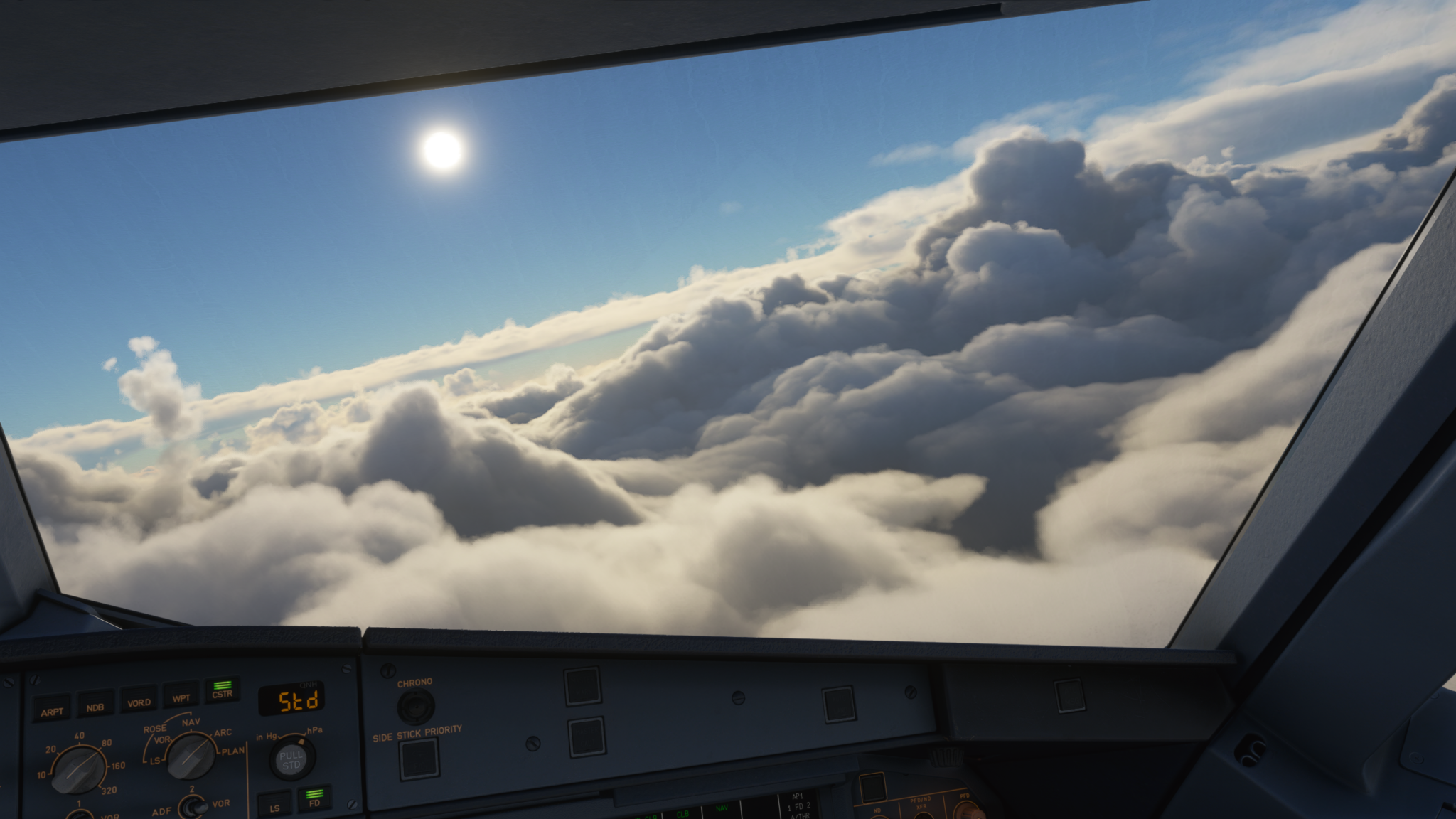
Hi everyone!
Hope you’ve all had an excellent week! We’re back to cover off another set of feature reviews, this time focusing on the fuel and hydraulic systems we’ve built into this A320. Last week we covered some software based items, and this week, we’ll look more at some of the physical or mechanical simulation we’ve incorporated into this airplane. This is a very, very dense technical update – so proceed with caution!
We’ll begin with the hydraulic simulation. Our hydraulic simulation goes a little further than simply telling the airplane whether something is pressurised or depressurised. In order to obtain proper failure simulation, the system must be built in a way where failures aren’t simply programmed. They are approached as an effect on a completely simulated system, as opposed to a set of programming instructions on what should happen. Instead, when all physically modelled hydraulic systems are accurate, they will automatically respond the way the real aircraft does to abnormal situations. This allows you to look deeper into why certain parts of the airplane do what they do, and respond the way they do. Every valve, pump, sensor, probe, cylinder, reservoir, control computer, accumulator, and more, is modelled with the correct behaviours and responses to abnormal situations caused by mishandling the airplane, or failures that you may choose to trigger. We’ve even modelled the piping used by the hydraulic fluid as it moves through the airplane, and the sensors that feed you with information are positioned correctly along these pipes to give you an accurate picture of what your airplane is doing. Some sensors cannot detect specific issues as they are upstream or downstream from where the issue is occurring – and this is modelled. Of course, the hydraulic fluid itself is modelled, with quantity, pressure and more existing in a physical simulation. The fluid moves from pipe to pipe, area to area, and in and out of the various hydraulically driven components.
An example, then. The leak measurement valves are part of the core hydraulic system, which reside in the wing spar (where the PTU is). Lines on which hydraulically driven components reside will have these leak measurement valves, usually used by ground personnel. These valves are accessible on the aft overhead, and can be closed (or switched off), which allows you to isolate hydraulically driven components on that line. You end up with no pressure in most hydraulically driven components, yet you have a completely normal reading of 3000 PSI on your lower ECAM HYD page. Bizarre? Absolutely. This occurs, however, due to the pressure sensor providing this value residing before the leak measurement valve – and when that is closed – the sensor is still reading a completely normal amount of pressure, even though the systems are isolated and everything after the valve (i.e most components) is depressurised.
So, if the airplane has depressurised lines after the leak measurement valves, yet it is indicating nominal pressure – how does it know to color part of the ECAM HYD synoptic amber – and more importantly, how does it know to give you all those ECAM warnings about depressurised components despite the nominal indication? Well, there’s another sensor right after the leak measurement valve. This sensor is hooked into the ECAM, which gives you a better idea of the “real” status of the components’ hydraulic status. This sensor does NOT provide the value of the system pressure to the lower ECAM, it simply warns of “LO” pressure – and therefore colors the line amber, and provides all the requisite warnings on the upper ECAM. On the opposite end of the spectrum, the sensor before the leak measurement valve is NOT linked to the ECAM and therefore does not give you any ECAM warnings as such. This sensor only provides a value, and should this sensor cease to work, the information it provides would simply be omitted – and the ECAM would display amber crosses in lieu of the value of HYD pressure. This can be seen if you simply pull the circuit breaker (C11) for this sensor and inhibit it, as demonstrated. The ECAM doesn’t panic, it simply omits the value. A low pressure warning would only be generated by the sensor after the leak measurement valve. The information presented to you in the flightdeck seems incredibly simple on the face of it, just some pressure indications after all, right? Underneath, however, a labyrinth. This is the level to which the Fenix A320 is simulated.
A video demonstrating the above!
Touching very quickly on the control surfaces, they are all driven via this complex hydraulic system simulation, allowing us to degrade and upgrade control surface movement and efficacy based on the hydraulic availability. As seen in the image below, the flaps are driven via two hydraulic inputs – Green and Yellow. These inputs go into a differential gearbox, which then drives the flaps. If you switch off (or fail) one of these hydraulic systems, the gearbox will only be receiving a single input, causing it to drive the flaps at half (or thereabouts) the speed! This is, of course, all simulated in the Fenix A320, as demonstrated above in the video! As a bonus, I show off the spoiler animations and degraded spoiler capability as a result of the yellow system being inoperable.
A further video demonstrates what occurs in the case of a complete loss of Blue and Green hydraulic systems, rendering only Yellow remaining to drive what’s left of the control surfaces on the airplane, and the degradation that follows. As mentioned before, we are driving all surfaces correctly via the hydraulics, allowing this deep level of degradation!
The next video here shows the interaction between the alternate braking system, and watching hydraulic fluid draining from the accumulator in the event the Yellow system is inoperable. Shown here is also the interaction between other parts of the airplane having a cause and effect on items you would have never thought interacted with one another – in this case, the opening of the FWD cargo door automatically triggering a short pulse of the Yellow electric pump, temporarily allowing the brake accumulator to recharge via the Yellow lines despite having a powered down Yellow engine driven pump!
A final word on the hydraulics and brakes – we’ve modelled the effects of time on the accumulator. With that, I mean – if you leave the airplane unattended for 24 hours or thereabouts with only it’s parking brake applied, the accumulator will slowly drain and eventually you’ll find your A320 rolling away slowly as the parking brake loses efficacy. This is why we use chocks in the real world!
Now we move on to the fuel side of this feature review. Now, naturally – we’ve handled fuel in a similar way as hydraulics, wherein the fuel and all of its requisite components are physically simulated – all the valves (high and low pressure), pumps, fuel sensors, and pipes are modelled – and the fuel itself is once again physically simulated right down to heat transfer mechanics. I mention heat transfer mechanics specifically as it leads me toward an interesting item I’d like to showcase – the IDG! In basic terms, the integrated drive generator (IDG) is a generator that resides within the engine structure and uses the engine itself to generate electricity in order to power the aircraft’s electrical systems. You may wonder what this has to do with the fuel – well, the IDG on board the A320 is cooled via the fuel. Nice, cold fuel on it’s way to the engine is run through the IDG to cool it, and in certain cases, such as low fuel demand at idle, this fuel may not be required in the engine’s combustion sequence, and is therefore piped back into the outer wing tanks, to then be cycled into the inner wing tanks, ready to go back to the engine once again. This posits some interesting possibilities. In normal operations, this would be fine. Leave the aircraft at idle for several hours, however, and you may start seeing the fuel temperature begin to rise. This can be accelerated, as demonstrated in the video below, by overheating the IDG with a low amount of fuel in the wing tanks. The temperature for the tank tied to the overheated IDG starts to slowly climb, showing the heat transfer mechanics at work!
We’ve also modelled the pump logic in great detail, looping back around to the IDG scenario – one may wonder where fuel goes when the wing tanks are completely full, and the airplane is feeding from the center tanks. It would simply overfill, causing all sorts of havoc. Well, in this scenario, the pump logic dictates that the fueling system must make some space for itself, so it switches BACK into the wing tanks, and consumes around 500kg of fuel from each, before the logic circuit switches the airplane back into feeding from the center tanks. Very cool stuff, and part of the incredible automation on board this airplane.
Some valve detail, now. We’ve modelled every valve this airplane has, but two particularly interesting valves are the low and high pressure valves near the engine. The low pressure valve resides in the engine pylon, whereas the high pressure valve is deeper, near the injectors. Any time you’re moving the engine master switches, both these valves open or close together depending on your switch position. When moving the switch to the cutoff position and shutting down an engine, it is the high pressure valve closing that causes the immediate engine cut. What’s particularly interesting about this is that there are certain scenarios in which one is unable to close the valves and shut the engine down, forcing you to close a low pressure valve (the high pressure valve cannot be closed in any other way, but the low pressure valve can be manually closed by pushing the engine fire PB on the overhead) in order to shut down an engine. It is also a great way to observe the physical modelling of the fuel – as closing the low pressure valve means there is still residual fuel circulating in the engine itself (remember I spoke about the positioning of these valves?) that needs to be consumed before the engine inevitably runs out of fuel and shuts down.
I will save this from getting much deeper (sorry for those of you who have already fallen asleep!), but this is a pretty solid insight into the lengths we have gone to in order to provide a holistic simulation of the A320 – drawing the correct lines and RF legs on the ND is one thing, valve simulation is another. Both together, however, create a complete simulation!
Someone needs to remind me to turn off my landing lights at FL100…
Have a great weekend, and feel free to drop by our Discord to say hello to the team!
Thanks,
Aamir